Insights and Innovations in Industrial Cleaning
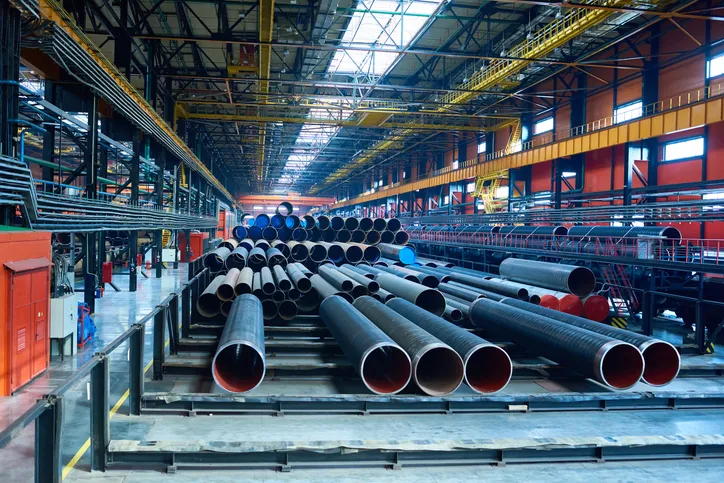
Efficient Cleaning Practices for Large Industrial Sites
Key Practices for Reducing Downtime
In large-scale industrial environments, cleanliness is crucial not only for operational efficiency but also for maintaining health and safety standards. A clean, well-maintained facility reduces the risk of accidents, contamination, and costly breakdowns, which can negatively affect production schedules. Christchurch’s industrial sector—ranging from food processing plants to manufacturing and logistics centers—relies heavily on maintaining cleanliness to meet both regulatory requirements and operational demands.
To maintain a clean facility without hindering ongoing operations, companies must adopt efficient cleaning protocols that minimize downtime and disruptions. These protocols, when designed effectively, can help businesses remain compliant with New Zealand’s health, safety, and environmental standards, while also maximizing productivity.
Best Practices for Industrial Cleaning Efficiency
1. Scheduling During Off-Peak Hours
One of the simplest yet most effective strategies for maintaining cleanliness in large-scale industrial environments is to schedule cleaning during off-peak hours. Cleaning during non-operational or low-traffic times helps avoid interference with the facility’s regular workflow.
2. Zone Cleaning
For large industrial facilities, implementing a zone cleaning approach can greatly enhance efficiency. Dividing the facility into smaller, manageable zones allows cleaning teams to work continuously without disrupting other parts of the operation. This method ensures that while one section is being cleaned, other areas can continue operating as usual.
3. Preventive Maintenance of Cleaning Equipment
Regular preventive maintenance of cleaning equipment ensures that machines remain in peak operating condition, reducing the likelihood of breakdowns during critical cleaning times. Downtime due to equipment failure can cause significant delays, especially in industries that rely heavily on automated scrubbers and sweepers for their cleaning tasks.
4. Proper Debris Removal Before Sweeping
Before any sweeping operation begins, it is crucial to remove large debris from the cleaning area to prevent damage to sweeping machines. Items such as shrink wrap, cardboard, and wood pose significant risks to the equipment. For instance, shrink wrap is notorious for causing damage to sweepers—it can be sucked up into the machine, working its way into the motor or other mechanical components, causing thousands of dollars in damage. Failing to clear the area of these materials can lead to costly repairs and prolonged downtime.
Risks of Not Clearing Debris:
- Poor results: Larger debris such as cardboard, wood, or metal fragments can get stuck in the squeegee, damaging it and requiring replacement. Additionally, debris stuck in the squeegee can leave streaks on the floor surface, reducing cleaning quality.
- Equipment malfunction: Debris that isn't suitable to be swept up can result in machine malfunction which can halt cleaning operations and cause costly delays in the facility's productivity.
- Equipment failure: Shrink wrap can entangle parts of the sweeper's motor or fan system, leading to severe damage and mechanical failure.
Clearing the area before sweeping is a fundamental step that cannot be overlooked, as it ensures the smooth operation of sweeping machines and reduces the risk of unexpected breakdowns.
5. Thorough Sweeping Before Wet Scrubbing
For facilities where wet scrubbing follows sweeping, the quality of sweeping directly impacts the effectiveness of the scrubbing process. If the floor is not properly swept beforehand, it can cause multiple issues for the scrubbing machine, including:
- Debris stuck in the squeegee: Larger pieces of debris can get caught in the squeegee, causing damage and leading to streaks being left on the floor surface.
- Decreasing cleaning quality: Dust and small particles can remain on the surface, compromising the effectiveness of the scrubbing operation.
- Damaging the scrubbing machine: Larger pieces of debris that are missed during sweeping can damage brushes and pads, leading to higher maintenance costs and machine downtime.
To avoid these problems, the area should be thoroughly swept before any scrubbing takes place, ensuring that the scrubber can operate at full efficiency and deliver high-quality cleaning results.
6. Training and Safety in Chemical Handling
At CanSweep, all of our operators are fully trained in chemical handling and safety. This training ensures that chemicals are used in the correct concentrations and applied in the safest manner, minimizing risks to both personnel and the environment. By following strict chemical handling protocols, we prevent any hazardous spills or improper usage, protecting both your facility and our operators.
7. Floor Surface Considerations
An often-overlooked factor in industrial cleaning is the condition of the floor surface being cleaned. No matter how efficient the cleaning machine, if the surface is pitted, cracked, or uneven, water can pool in these areas, making it difficult for scrubbers to effectively dry the floor. Pooled water not only affects the overall cleanliness but can also lead to long-term damage to the floor surface.
Regular sweeping of concrete areas can help prevent the deterioration of the floor by removing debris that would otherwise be ground in by forklift or truck movements, causing wear and tear over time. Ensuring that the floor surface is properly maintained and smooth can greatly improve the efficiency of both sweeping and scrubbing operations, reducing the need for frequent repairs or maintenance.
8. Modern Scrubbing Machines Leave Floors Drier
Another critical aspect of industrial cleaning is the drying process after scrubbing. Older, outdated scrubbing machines often leave floors wet, which can cause safety hazards or operational delays as workers wait for the surface to dry. At CanSweep, we use newer scrubbing machines that are designed to leave floors drier than older models.
Conclusion
Efficient cleaning protocols are essential for maintaining operational continuity in Canterbury's large-scale industrial environments. By adopting best practices such as scheduling cleaning during off-peak hours, zone cleaning, regular equipment maintenance, clearing debris prior to sweeping, properly managing chemicals, and considering floor surface conditions, businesses can significantly reduce downtime, enhance operational efficiency, and ensure compliance with health and safety standards.
At CanSweep, we are committed to delivering the highest quality industrial cleaning services using modern equipment, environmentally friendly chemicals, and a well-trained workforce. These practices not only improve the working environment but also contribute to the long-term sustainability and competitiveness of New Zealand’s industrial sectors.